Aug 19, 2024
Thermal Transfer Printers: Cleaning, Maintenance & Troubleshooting
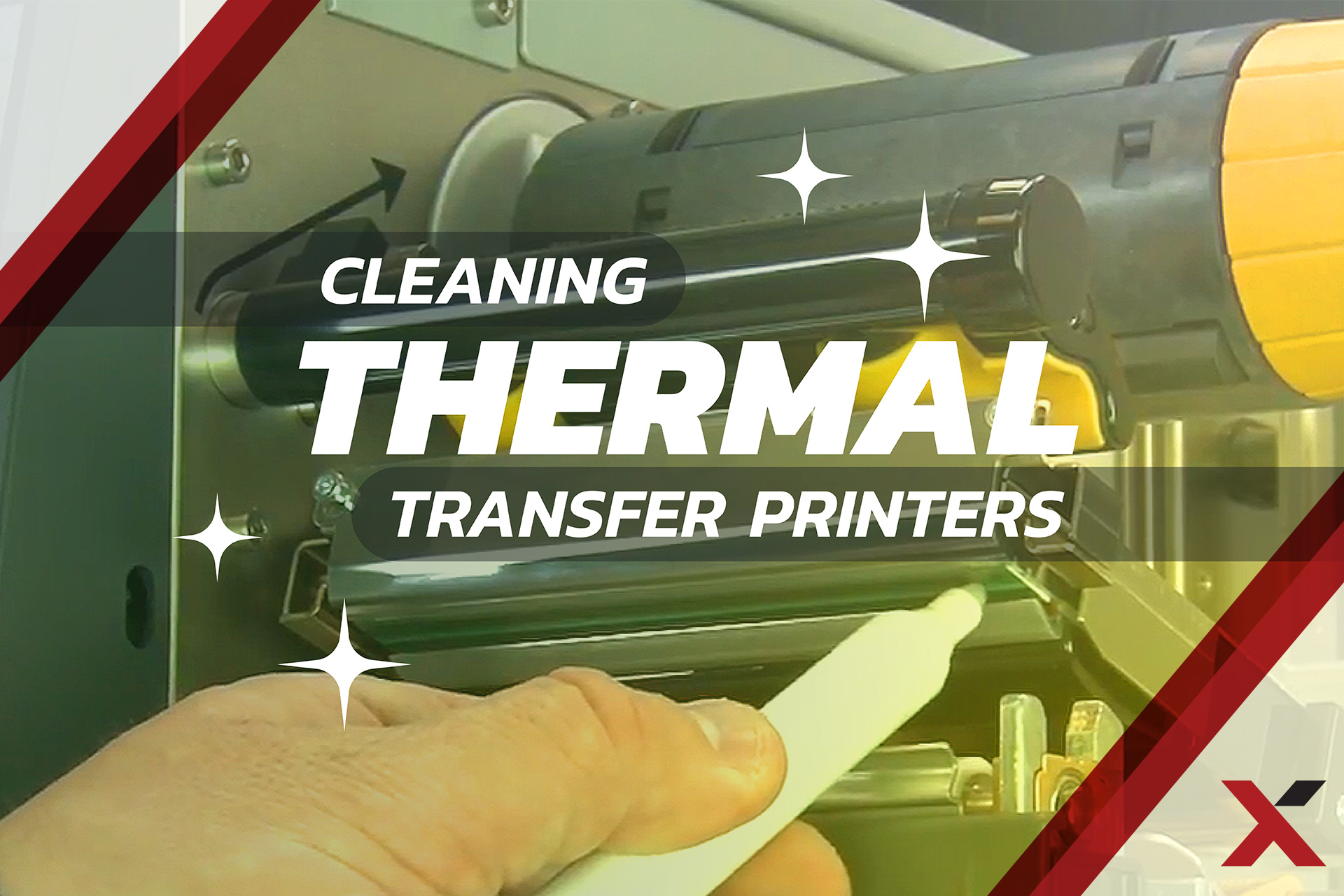
Thermal transfer printers are tough little beasts – and it’s easy to forget to give them proper care. Are your thermal printers getting regular service?
Proper cleaning, maintenance, and troubleshooting are crucial to ensure these printers continue to operate efficiently and produce high-quality results. And the last thing your operation needs is for a barcode printer or a label maker to get cranky in the middle of a busy day.
These tips will help you maintain your thermal transfer printer and resolve common issues.
Cleaning Your Thermal Transfer Printer
Regular cleaning prevents build-up that can affect print quality and extend the life of your printer. Here’s how to keep your thermal transfer printer in top shape:
- Clean the Print Head:
- Why: Residue from the ribbon and label material can build up on the print head, affecting print quality and causing printhead damage.
- How:
- Turn off the printer and let it cool down.
- Open the printer to access the print head.
- Use a soft, lint-free cloth lightly dampened with isopropyl alcohol (preferably 99%) or a dedicated print head cleaning pen.
- Gently wipe the print head to remove any residue. Avoid using abrasive materials or excessive force.
- Clean the Platen Roller:
- Why: The platen roller, which helps move the label through the printer, can accumulate dirt and adhesive residue, causing feeding issues and uneven printing.
- How:
- After turning off the printer, access the platen roller.
- Use a lint-free cloth with a small amount of isopropyl alcohol to wipe the roller clean.
- Inspect the roller for any cracks or damage. Replace if necessary.
- Clean the Sensors:
- Why: Sensors detect label gaps and alignment. Dust or adhesive residue can obstruct their function.
- How:
- Locate the sensors, usually near the print head or inside the printer.
- Use a soft cloth with isopropyl alcohol to gently clean the sensors.
- Avoid getting any alcohol on other parts of the printer.
- Check for Adhesive Build-Up:
- Why: Labels can leave adhesive residue that accumulates over time and affects print quality.
- How:
- Regularly inspect areas where labels are fed through and ensure there’s no build-up.
- Clean these areas with a damp cloth or cleaning wipe.
Routine Maintenance Tips
- Regularly Inspect and Replace Parts:
- Why: Over time, parts like the print head and platen roller can wear out and affect print quality.
- How:
- Check these parts for wear and tear during your cleaning routine.
- Follow the manufacturer’s recommendations for replacement intervals and use genuine parts to ensure compatibility and performance.
- Calibrate Your Printer:
- Why: Calibration ensures that your printer accurately measures label gaps and aligns the print.
- How:
- Consult your printer’s manual for calibration procedures, as they vary by model.
- Generally, calibration involves running a test print or using the printer’s menu to align the sensors and adjust the label feed.
- Update Firmware:
- Why: Firmware updates can fix bugs, improve performance, and add new features.
- How:
- Check the manufacturer’s website for the latest firmware version for your printer model.
- Follow the instructions to update the firmware, usually involving downloading the update and following on-screen prompts.
- Monitor Ribbon and Label Usage:
- Why: Incorrect ribbon or label types can affect print quality and cause printer malfunctions.
- How:
- Use the ribbon and labels recommended by the manufacturer.
- Store ribbons and labels in a clean, dry place to avoid contamination.
Troubleshooting Common Issues
Poor Print Quality:
- Symptoms: Faded prints, missing information, or streaks.
- Solutions:
- Check Print Head: Clean the print head as described above. If the issue persists, the print head may need replacement.
- Adjust Print Darkness and Speed: Increase the darkness setting if the print is too light, and slow down the print speed for better quality.
- Check Ribbon and Labels: Ensure you’re using the correct ribbon for your label type and that it’s loaded correctly.
Skipping Labels:
- Symptoms: The printer skips labels or misfeeds.
- Solutions:
- Inspect Label Path: Make sure labels are loaded correctly and aligned with the printer guides.
- Run Calibration: Perform a calibration to ensure the printer correctly detects label gaps and alignment.
- Clean Sensors: Dust or residue on sensors can cause feeding issues. Clean the sensors thoroughly.
Printer Not Responding or Error Messages:
- Symptoms: The printer fails to start, displays error messages, or stops mid-print.
- Solutions:
- Check Connections: Ensure all cables and connections are secure.
- Restart the Printer: Turn off the printer, wait a few seconds, and turn it back on.
- Consult the Manual: Refer to the error codes in your printer’s manual for specific troubleshooting steps.
Ribbon Issues:
- Symptoms: Ribbon wrinkling, breaking, or not feeding properly.
- Solutions:
- Adjust Ribbon Tension: Ensure the ribbon is properly tensioned and aligned.
- Check Ribbon Path: Make sure the ribbon is feeding through the printer correctly.
- Replace Worn Parts: If the ribbon is consistently problematic, check for worn parts or consider using a different ribbon type.
Settings Not Saving:
- Symptoms: Printer settings revert to default or previous settings after making changes.
- Solutions:
- Check Software Settings: Make sure the label design software or driver settings match your printer settings.
- Use Printer Settings: In the printer driver preferences, select "Use Printer Settings" to ensure changes are applied directly to the printer.
These tips will cover 90% of the issues you might have with your thermal transfer printer. That said, each device will have its unique quirks and specific solutions.
Have you considered outsourcing your printer maintenance? As the nation’s largest privately-held, brand-neutral managed print services provider, we have a large army of expert technicians ready to service your printing devices.
Reach out to us today for an assessment.